智能传感实时监测
库卡焊接机器人搭载高精度传感系统,是实现节气的基础。焊接过程中,传感器持续监测焊接电流、电压、焊接速度、电弧形态以及熔池温度等关键参数。这些参数的变化直接反映焊接工况对保护气体需求的差异。例如,焊接起始阶段,电流较小,电弧较弱,此时系统感知到焊接需求变化,为节气调控提供依据;当焊接进入高速或厚板焊接阶段,电流增大,传感器快速捕捉参数波动,及时反馈给控制系统,使机器人能针对不同焊接工况做出精准响应,为后续节气操作奠定基础。
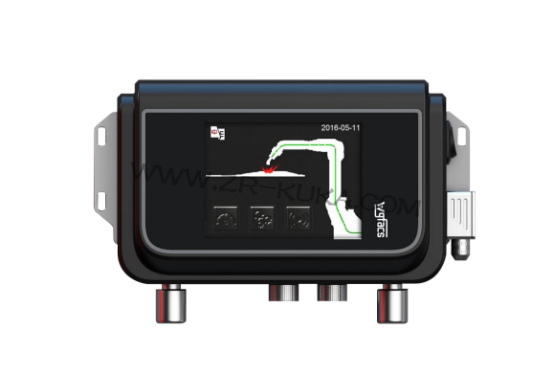
基于传感器实时采集的数据,库卡焊接机器人的控制系统通过动态调控机制实现节气。当判断焊接工况对保护气体需求降低时,如在焊接薄板或低速焊接阶段,系统自动调节保护气阀门开度,减少气体输出流量。同时,根据不同焊接工艺与材料特性,对混合气中各气体成分比例进行优化调整。在 MIG 焊接碳钢薄板时,降低惰性气体比例,增加活性气体比例,既能满足焊接保护需求,又减少气体浪费。而在焊接厚板等需要大流量保护气的工况下,系统及时增大气体流量,确保焊接区域得到充分保护,在保证焊接质量的前提下,实现保护气体的精准适配与高效节约,推动kuka机器人节气目标达成。
算法优化智能决策
库卡焊接机器人内置先进算法,为节气提供智能决策支持。该算法基于大量焊接工艺数据与经验,能够快速分析传感器采集的参数信息,预测焊接过程中保护气体的需求变化趋势。在焊接路径发生变化或材料厚度出现过渡时,算法提前规划保护气流量与成分的调整策略,使系统在工况变化前就做出相应调节,避免气体浪费。算法还具备自学习能力,可根据实际焊接效果不断优化控制策略,随着使用时间增长,库卡焊接机器人节气效果不断提升,持续为企业节省保护气体成本。
KUKA 库卡焊接机器人通过智能传感实时监测、动态调控精准适配与算法优化智能决策三大核心原理,实现保护气体的高效节约。这些原理相互协作,不仅降低企业生产成本,更保障焊接质量稳定,为工业焊接领域的可持续发展注入动力,充分体现kuka焊接机器人节气的技术价值与应用潜力。